Professional Advice on What is Porosity in Welding and Just How to Address It
Professional Advice on What is Porosity in Welding and Just How to Address It
Blog Article
Porosity in Welding: Identifying Common Issues and Implementing Best Practices for Avoidance
Porosity in welding is a pervasive problem that commonly goes undetected up until it creates significant issues with the stability of welds. This typical issue can compromise the strength and longevity of bonded frameworks, positioning security dangers and bring about pricey rework. By understanding the origin of porosity and executing efficient prevention methods, welders can dramatically improve the high quality and dependability of their welds. In this discussion, we will explore the crucial variables adding to porosity development, examine its damaging impacts on weld performance, and discuss the most effective practices that can be adopted to lessen porosity event in welding processes.
Usual Reasons of Porosity

Using filthy or wet filler products can introduce contaminations right into the weld, contributing to porosity issues. To mitigate these usual causes of porosity, thorough cleaning of base metals, correct shielding gas selection, and adherence to optimal welding criteria are essential practices in attaining high-quality, porosity-free welds.
Impact of Porosity on Weld Quality

The presence of porosity in welding can dramatically endanger the architectural honesty and mechanical residential properties of bonded joints. Porosity develops voids within the weld steel, compromising its general strength and load-bearing capability.
Welds with high porosity degrees tend to show lower impact stamina and decreased ability to flaw plastically before fracturing. Porosity can hamper the weld's ability to successfully transfer pressures, leading to premature weld failure and prospective safety threats in critical structures.
Ideal Practices for Porosity Avoidance
To boost the architectural integrity and high quality of bonded joints, what details measures can be executed to minimize the event of porosity throughout the welding process? Making use of the right welding strategy for the certain material being bonded, such as adjusting the welding angle and gun placement, can better stop porosity. Regular inspection of welds and prompt removal of any type of concerns recognized during the welding process are crucial methods to avoid porosity and produce top quality welds.
Importance of Proper Welding Methods
Implementing correct welding methods is critical in ensuring the structural integrity and quality of welded joints, building upon the foundation of efficient porosity avoidance procedures. Excessive warm can lead to increased porosity due to the entrapment of gases in the weld pool. In addition, using the appropriate welding specifications, such as voltage, existing, and take a trip rate, is important for attaining sound welds with minimal porosity.
In addition, the selection of welding process, whether it be look at this website MIG, TIG, or additional info stick welding, need to straighten with the certain needs of the project to guarantee optimal outcomes. Proper cleansing and prep work of the base steel, as well as picking the right filler material, are additionally important elements of competent welding strategies. By sticking to these ideal techniques, welders can lessen the danger of porosity formation and create top quality, structurally audio welds.
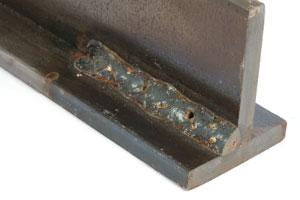
Testing and Top Quality Control Measures
Evaluating procedures are vital to discover and protect against porosity in welding, making sure the toughness and longevity of the last item. Non-destructive screening methods such as ultrasonic screening, radiographic screening, and visual evaluation are commonly utilized to identify potential flaws like porosity.
Post-weld assessments, on the various other hand, assess the final weld for any kind of flaws, including porosity, and confirm that it fulfills defined standards. Applying a thorough quality control strategy that consists of thorough testing treatments and examinations is vital to reducing porosity concerns check my site and guaranteeing the general top quality of welded joints.
Verdict
Finally, porosity in welding can be an usual problem that affects the quality of welds. By recognizing the common sources of porosity and applying best techniques for prevention, such as proper welding techniques and testing actions, welders can make sure high quality and reputable welds. It is vital to prioritize avoidance methods to lessen the occurrence of porosity and keep the stability of bonded frameworks.
Report this page